What is five Axis CNC Machining
2015-01-07 23:42:04
Five axis computer numerical control (CNC) systems are able to move internal tools in three primary axes, designated X, Y, and Z, and two more axes created by the rotation of the X and Y axes. These axes lie parallel to the tool spindle, a core component of CNC production machines. Five axis CNC machining is intended for making complex, three-dimensional parts such as turbine blades, impellers, and tools for plastic molding. The aerospace, oil and gas, woodworking, mold making, medical, and energy production industries regularly use CNC machining.
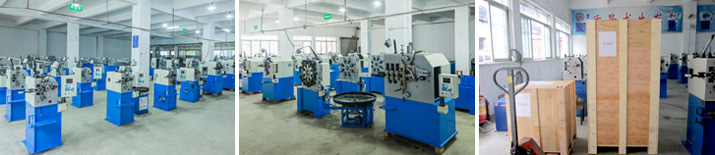
With five axis CNC machining, the process of machining these parts occurs automatically. The system is set up at the beginning of production and runs according to what has been programmed into it until the process is finished. A piece of equipment known as a machining center, which is sold as horizontally or vertically oriented, is required. Whether to choose a horizontal or vertical machining center depends on the application and space available in a factory or other facility, but these are not average home-based machines. They can go for over $1,000,000 US Dollars (USD) apiece.
The capabilities of a five axis CNC machining center are enhanced by spindle head attachments. These increase the accuracy and add capabilities, such as 90° and 360° ranges of motion, for rotary applications. Spindle heads are often programmable and operate over the machine’s total work envelope, meaning that they can reach anywhere within the machining center where any milling takes place.
Five axis CNC machining has a few benefits despite the cost of the equipment and expertise needed to operate it. Parts do not have to be set up in different positions for different stages of the milling process, nor do parts have to be placed manually at various angles. The need for extra tools to keep the pieces steady at these angles is eliminated as well. Features can be added to parts and surfaces that could not be without five axis CNC machining equipment.
Compared to three-axis machining systems, shorter tools can be used and a part can be completed in far less time. The specified travels of each axis can far exceed the dimensions of many parts, and the use of spindle attachments in five axis CNC machining improves that capacity in general and when machining inside mold cavities. Parts do not need to be loaded or unloaded either, so the efficiency is much better in terms of time and resources.